1. Skref eitt: Bræðsla
Ál er framleitt með rafgreiningu í iðnaðar mælikvarða og álver þurfa mikla orku til að ganga vel.Álver eru oft staðsett við hlið stórvirkjana vegna orkuþörfarinnar.Öll aukning á orkukostnaði, eða magn afl sem þarf til að hreinsa ál í hærri einkunn, eykur kostnað við álspólur.Auk þess skilur ál sem hefur verið leyst upp og fer á söfnunarsvæði.Þessi tækni hefur einnig töluverða orkuþörf sem hefur einnig áhrif á álmarkaðsverð.
2. Skref tvö: Hot Rolling
Heitvalsing er ein algengasta leiðin til að þynna álplötu.Í heitvalsingu er málmur hitaður upp fyrir endurkristöllunarpunktinn til að afmynda hann og móta hann frekar.Síðan er þetta málmlager flutt í gegnum eitt eða fleiri pör af rúllum.Þetta er gert til að draga úr þykkt, gera þykkt einsleita og til að ná tilætluðum vélrænni gæðum.Álspóla er búin til með því að vinna blaðið við 1700 gráður á Fahrenheit.
Þessi aðferð getur framleitt form með viðeigandi rúmfræðilegum breytum og efniseiginleikum á meðan málmrúmmálinu er haldið stöðugu.Þessar aðgerðir skipta sköpum við framleiðslu á hálfgerðum og fullunnum hlutum, svo sem plötum og blöðum.Hins vegar eru fullunnar valsaðar vörur frábrugðnar kaldvalsuðum vafningum, sem verður útskýrt hér að neðan, að því leyti að þær hafa minna einsleita þykkt vegna örlítið rusl á yfirborðinu.
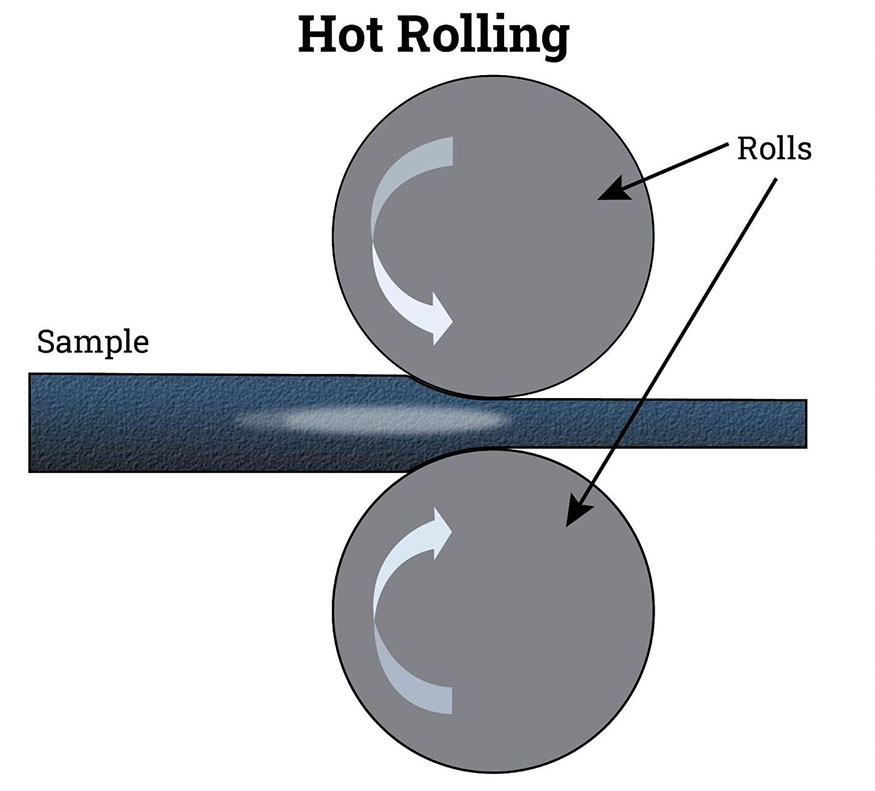
3. Skref þrjú: Kaldvalsing
Kaltvalsun málmræma er einstakt svæði í málmvinnslugeiranum.Ferlið við "kaldvalsingu" felur í sér að setja ál í gegnum kefli við lægra hitastig en endurkristöllunarhitastig þess.Með því að kreista og þjappa málminum eykst flæðistyrk hans og hörku.Kaltvalsing á sér stað við vinnuherðingarhitastig (hitastigið undir endurkristöllunarhitastigi efnis) og heitvalsing á sér stað yfir vinnuherðingarhitastiginu - þetta er munurinn á heitvalsingu og kaldvalsingu.
Margar atvinnugreinar nota málmmeðferðaraðferðina sem kallast kaldvalsing til að framleiða ræmur og málmplötur með tilætluðum lokamæli.Rúllurnar eru oft hitaðar til að auðvelda álið að vinna betur og smurefni er notað til að koma í veg fyrir að álræman festist við rúllurnar.Fyrir fínstillingu í vinnslu er hægt að breyta hreyfingu og hita rúllanna.Álræmur, sem þegar hefur verið heitvalsaður, og aðrar aðgerðir, þar á meðal hreinsun og meðhöndlun, er kæld niður í stofuhita áður en hún er sett í kaldvalslínu í áliðnaði.Ál er hreinsað með því að skola það með þvottaefni og þessi meðhöndlun gerir álspóluna nógu harða til að þola kaldvalsingu.
Eftir að búið er að taka á þessum undirbúningsskrefum fara ræmurnar endurteknar í gegnum rúllur og missa smám saman þykkt.Grindaplan málmsins eru trufluð og á móti í öllu ferlinu, sem leiðir til harðari og sterkari lokaafurðar.Kaltvalsing er meðal vinsælustu aðferðanna til að herða ál því það dregur úr þykkt áliðs þegar það er mulið og þrýst í gegnum rúllur.Kaldvalstækni getur lækkað þykkt álspólu um allt að 0,15 mm.
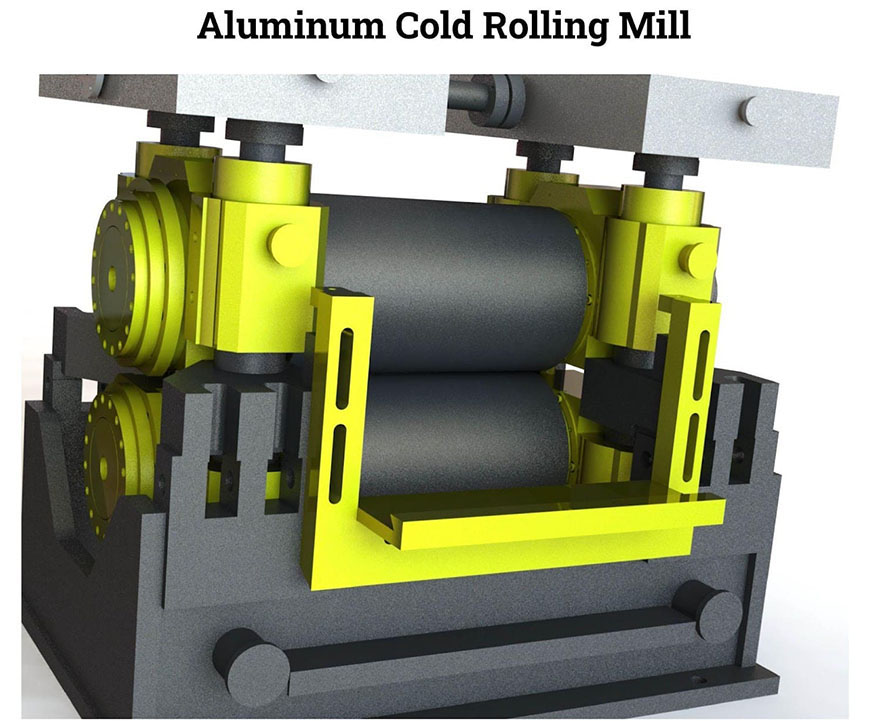
4. Skref Fjórða: Hreinsun
Glöðunarferli er hitameðferð sem notuð er fyrst og fremst til að gera efni sveigjanlegra og minna stíft.Minnkun á tilfærslum í kristalbyggingu efnisins sem verið er að glæða veldur þessari breytingu á hörku og sveigjanleika.Til að koma í veg fyrir brothætta bilun eða til að gera efni vinnsluhæfara fyrir eftirfarandi aðgerðir, er glæðing oft gerð eftir að efni hefur gengist undir herðingu eða kaldvinnslu.
Með því að endurstilla kristallaða kornabygginguna á áhrifaríkan hátt endurheimtir glæðing sleðaplan og gerir frekari mótun hlutans kleift án of mikils krafts.Vinnuhertu álblöndu verður að hita í ákveðið hitastig á milli 570°F og 770°F í fyrirfram ákveðið tímabil, allt frá um það bil þrjátíu mínútum til þriggja klukkustunda.Stærð hlutans sem verið er að glæða og málmblönduna sem hann er gerður úr ákvarða hitastig og tímaþörf, í sömu röð.
Gleðrun kemur einnig á stöðugleika í stærð hluta, útilokar vandamál sem stafa af innri álagi og dregur úr innri álagi sem getur myndast, að hluta til, við aðgerðir eins og köldu mótun eða steypu.Að auki er einnig hægt að glæða álblöndur sem ekki eru hitameðhöndlaðar.Þess vegna er það oft notað á steypta, pressaða eða smíðaða álhluta.
Geta efnis til að myndast eykst með glæðingu.Það getur verið krefjandi að þrýsta eða beygja hörð, brothætt efni án þess að valda beinbrotum.Glæðing hjálpar til við að fjarlægja þessa áhættu.Að auki getur glæðing aukið vélhæfni.Mikill stökkleiki efnis gæti leitt til of mikils slits á verkfærum.Með glæðingu er hægt að minnka hörku efnis, sem getur dregið úr sliti á verkfærum.Öll spenna sem eftir er er eytt með glæðingu.Venjulega er best að draga úr afgangsspennu þar sem það er mögulegt vegna þess að þær gætu leitt til sprungna og annarra vélrænna vandamála.
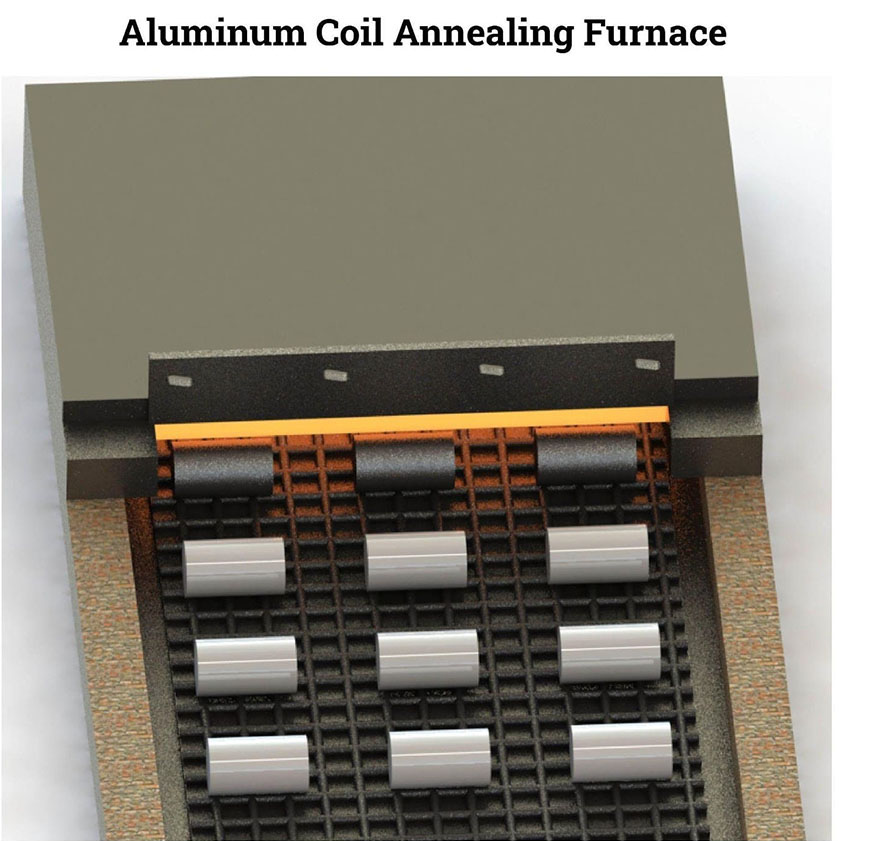
5. Skref fimm: Slit og klippa
Hægt væri að framleiða álspólur í einni mjög langri samfelldri rúlla.Til að pakka spólunni í smærri rúllur þarf hins vegar að skera þær í sneiðar.Til að framkvæma þessa aðgerð eru álrúllur keyrðar í gegnum skurðarbúnað þar sem ótrúlega skörp blöð gera nákvæma skurð.Mikið afl þarf til að framkvæma þessa aðgerð.Slits skipta rúllunni í smærri hluta þegar beitt kraftur fer yfir togstyrk áliðs.
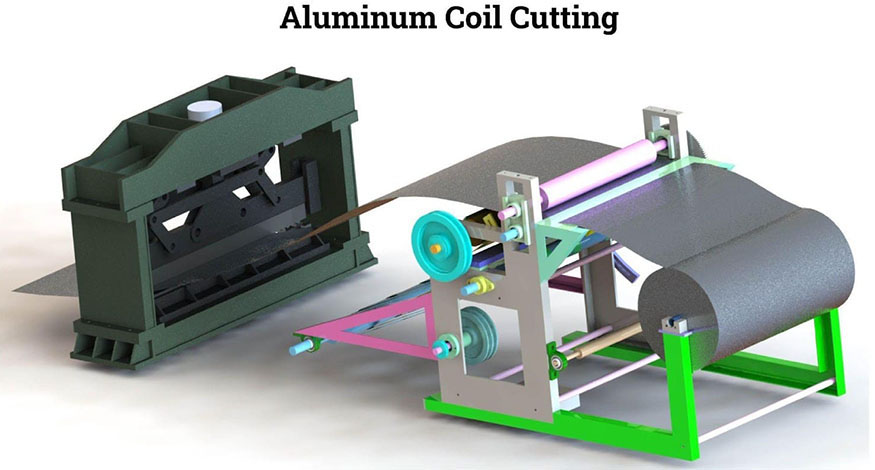
Til að hefja skurðarferlið er álið sett í uncoiler.Eftir það er því farið í gegnum sett af snúningshnífum.Blöðin eru staðsett til að fá bestu rifbrúnina, miðað við æskilega breidd og úthreinsun.Til að beina rifuefninu að recoilernum er efnið síðan borið í gegnum skiljur.Álið er síðan sett saman og vafið inn í spólu til að undirbúa sendingu.
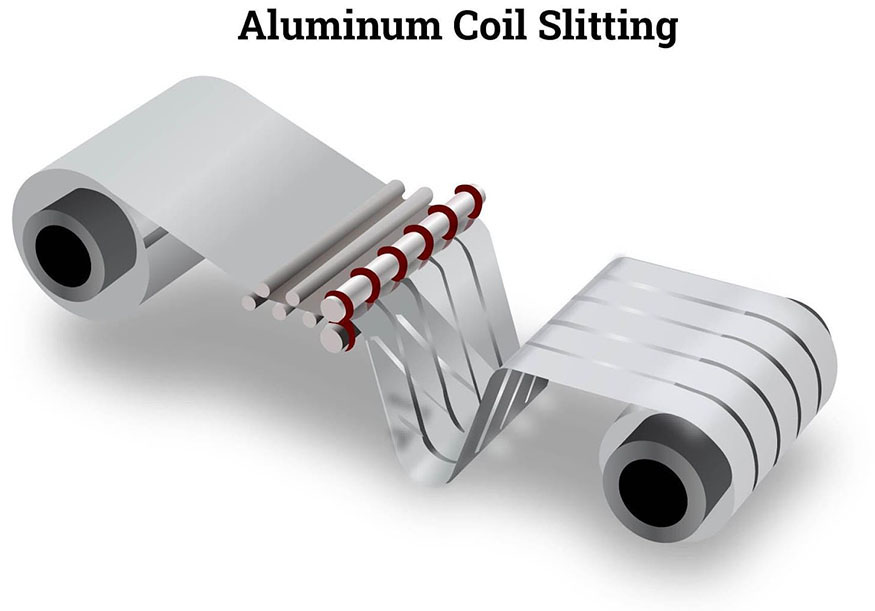
Jindalai Steel Group er leiðandi álfyrirtæki og birgir álspólu/plötu/plötu/ræma/pípa/þynnu.Við höfum viðskiptavini frá Filippseyjum, Thane, Mexíkó, Tyrklandi, Pakistan, Óman, Ísrael, Egyptalandi, Arabíu, Víetnam, Mjanmar, Indlandi o.s.frv. Sendu fyrirspurn þína og við munum vera fús til að ráðfæra þig við þig faglega.
SÍÐALÍNA:+86 18864971774WECHAT: +86 18864971774WHATSAPP:https://wa.me/8618864971774
PÓST:jindalaisteel@gmail.com sales@jindalaisteelgroup.com VEFSÍÐA:www.jindalaisteel.com
Birtingartími: 19. desember 2022